Conveyor Routing
Order Consolidation
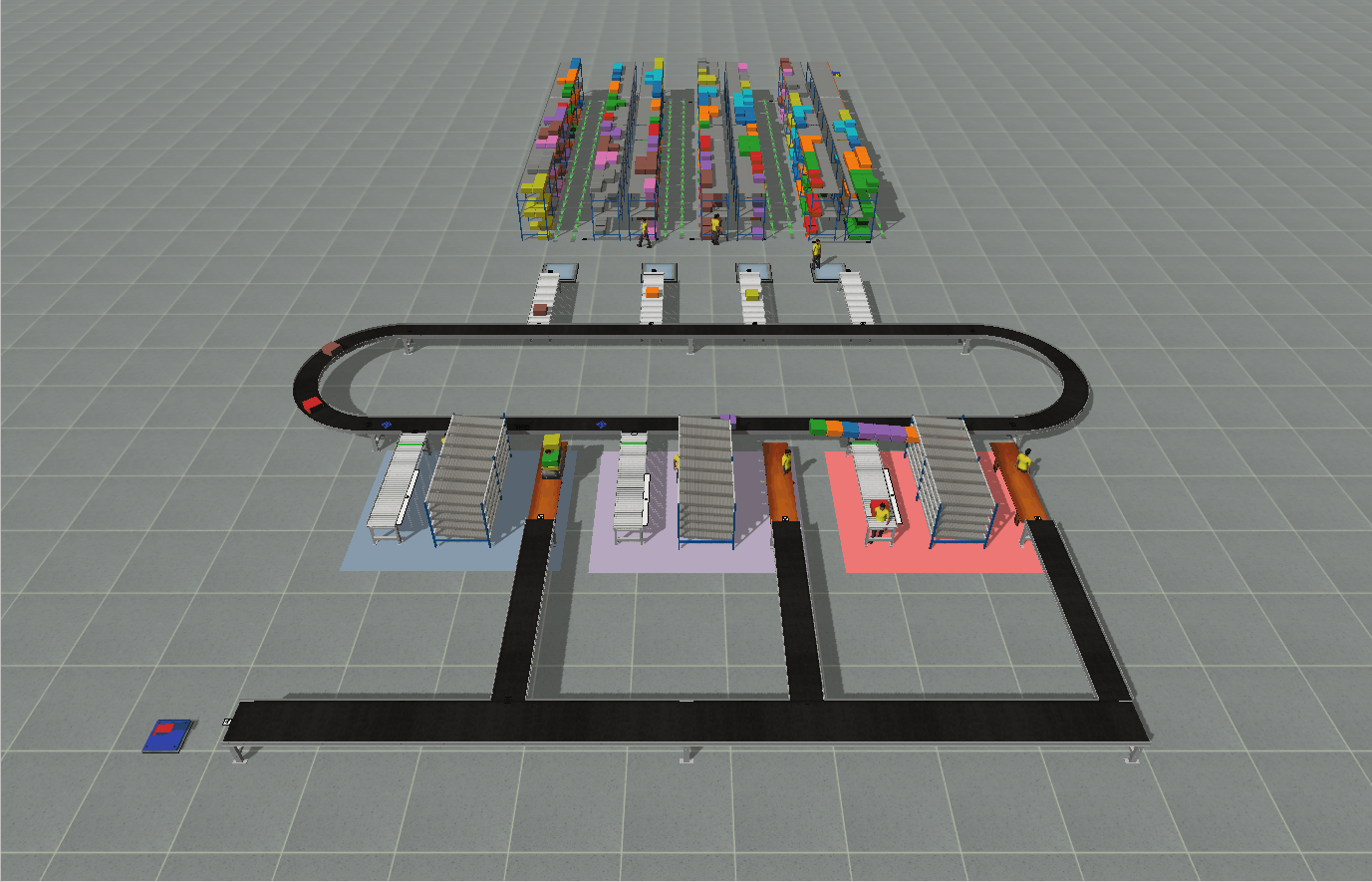
Project Overview
This project focuses on enhancing warehouse order-picking efficiency through the application of Discrete Event Simulation (DES) using FlexSim. It specifically addresses the challenges in optimizing conveyor routing order consolidation methodology to meet the increasing demands of e-commerce, especially during peak sales periods.
The project aims to create a more efficient and streamlined order-picking process by:
- Reducing travel distances for pickers
- Minimizing order processing times
- Improving resource utilization
- Enhancing accuracy in order fulfillment
Challenges and Solutions
The project addresses the complexities of warehouse management in the e-commerce era, which often involves:
- Managing high SKU (Stock Keeping Unit) volumes
- Facing stringent fulfillment time requirements
- Dealing with fluctuating demand patterns
To tackle these challenges, the project utilizes FlexSim's 3D modeling and process flow features to create a digital twin of the warehouse environment. This simulation model enables the exploration of different order consolidation strategies and conveyor routing configurations to identify the most efficient solutions.
Specifically, the project focuses on:
- Optimizing the placement of product zones to reduce picker travel distances
- Designing efficient conveyor routing paths to minimize transit times
- Implementing dynamic order batching to consolidate orders based on proximity and destination
Results and Impact
The implementation of DES via FlexSim has yielded significant improvements in various performance metrics, including:
- Throughput: The simulation model demonstrated a 15% increase in average throughput, from 93 orders to 115 orders, indicating a substantial boost in overall productivity.
- Travel Distance: The optimized conveyor routing and product zone placement led to a 22% reduction in average picker travel distances, saving valuable time and labor costs.
- Utilization: Picker utilization rates improved by 10%, suggesting a more efficient allocation of resources and a reduction in idle time.
- Order Processing Time: The average order processing time decreased by 18%, resulting in faster fulfillment and potentially improved customer satisfaction.
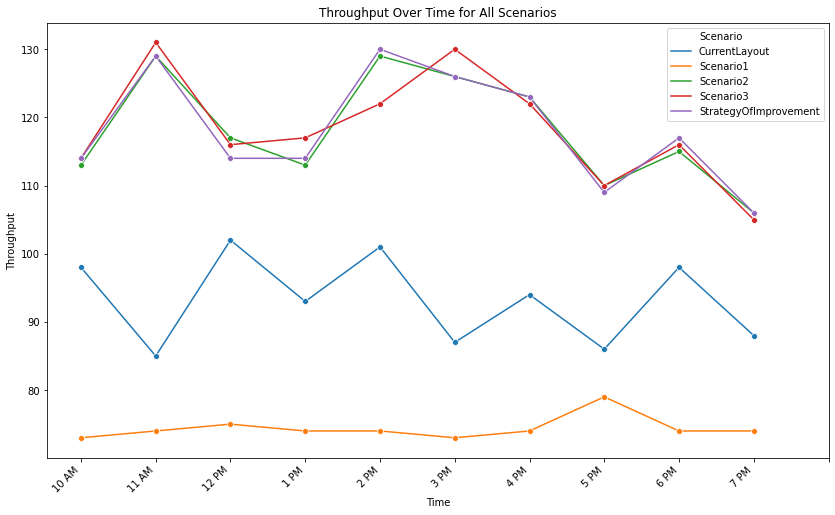
The analysis of throughput data over time revealed key insights, such as variations in performance and potential trends that can be further explored for optimization. Moreover, the utilization analysis highlighted the importance of efficient task allocation and potential areas for improvement. The travel distance analysis demonstrated the impact of layout and process changes on operator efficiency, suggesting opportunities for further optimization through layout modifications or automation.